Sustainability in the Alumeco Group
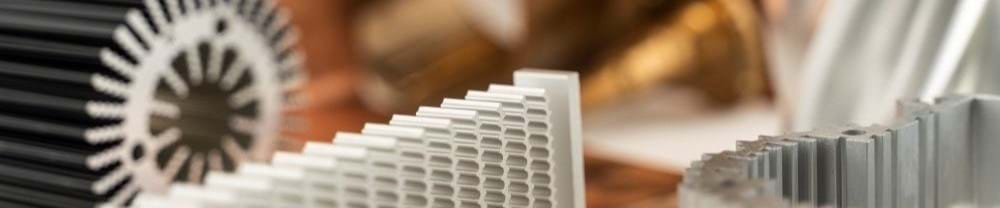
Limiting our impact on the planet
Running a business is not only about profit. We are also committed to the world around us. To support our goal of limiting our negative impact on people and planet, we have chosen to focus on four UN Sustainable Development Goals:
Based on these goals, our sustainability efforts are currently focused around three main areas (from short to long term):
- Our own climate footprint
- Our social impact in our local areas
- The climate footprint of our supply chain
You can follow our yearly progress in these areas in our corporate social responsibility reports.
Our goals
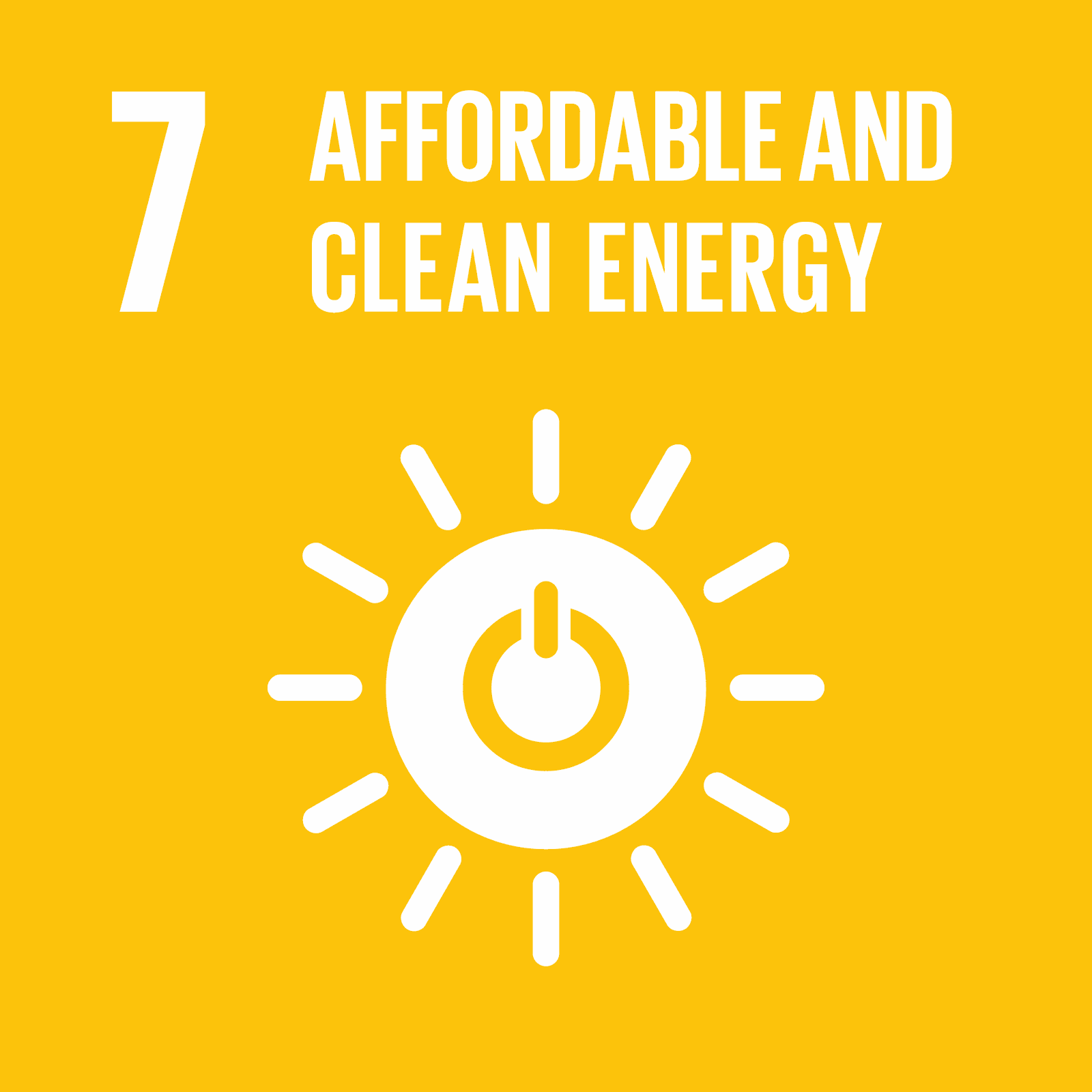
We aim to use 100% electricity from renewable sources by 2040.
We will do this in two streps:
- Reduce the energy demand in Alumeco Group
- Invest in renewable alternatives
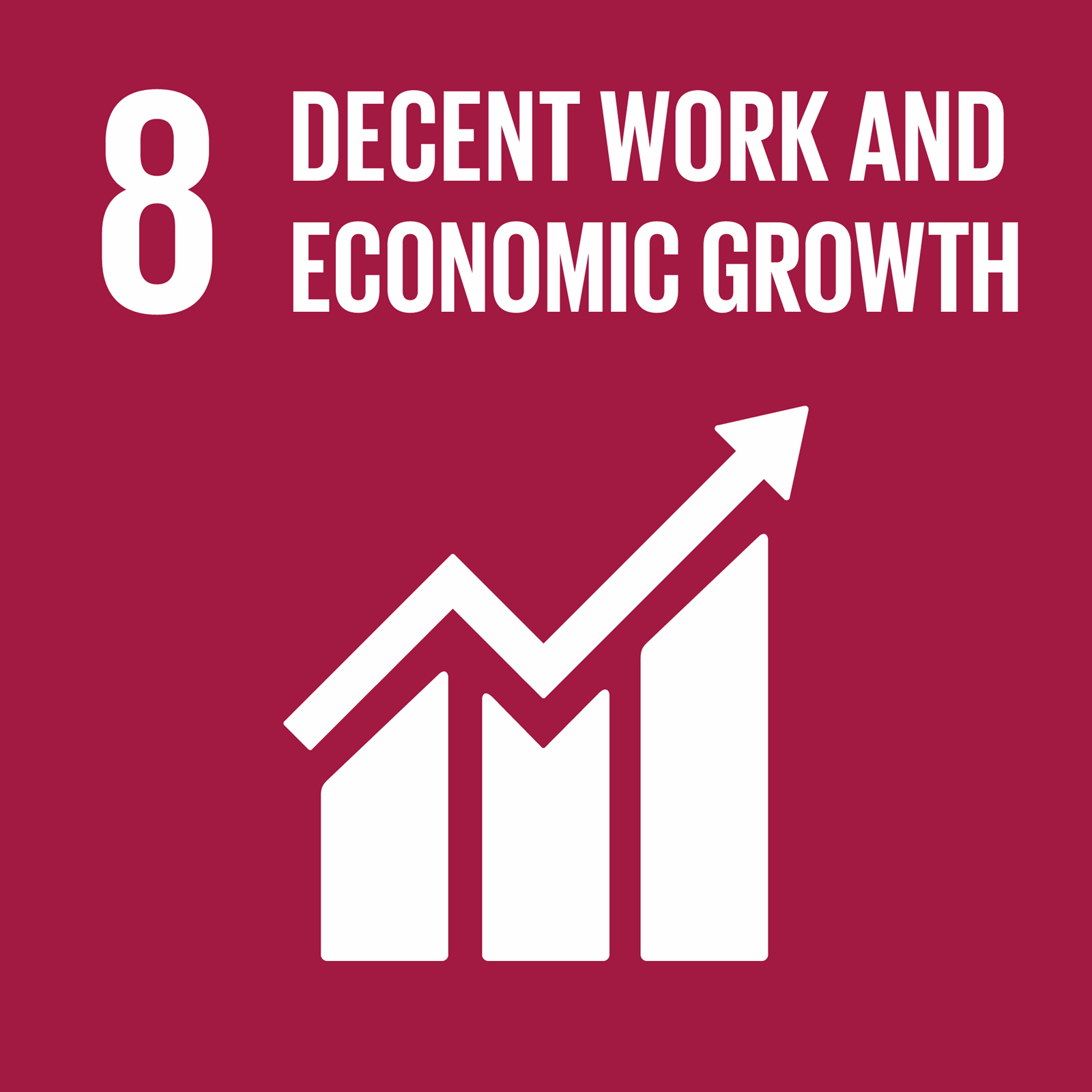
To guarantee high standards across the Alumeco Group, we are now ISO 45001-certified (work environment) in our four main warehouses (Poland, China, Germany and Denmark).
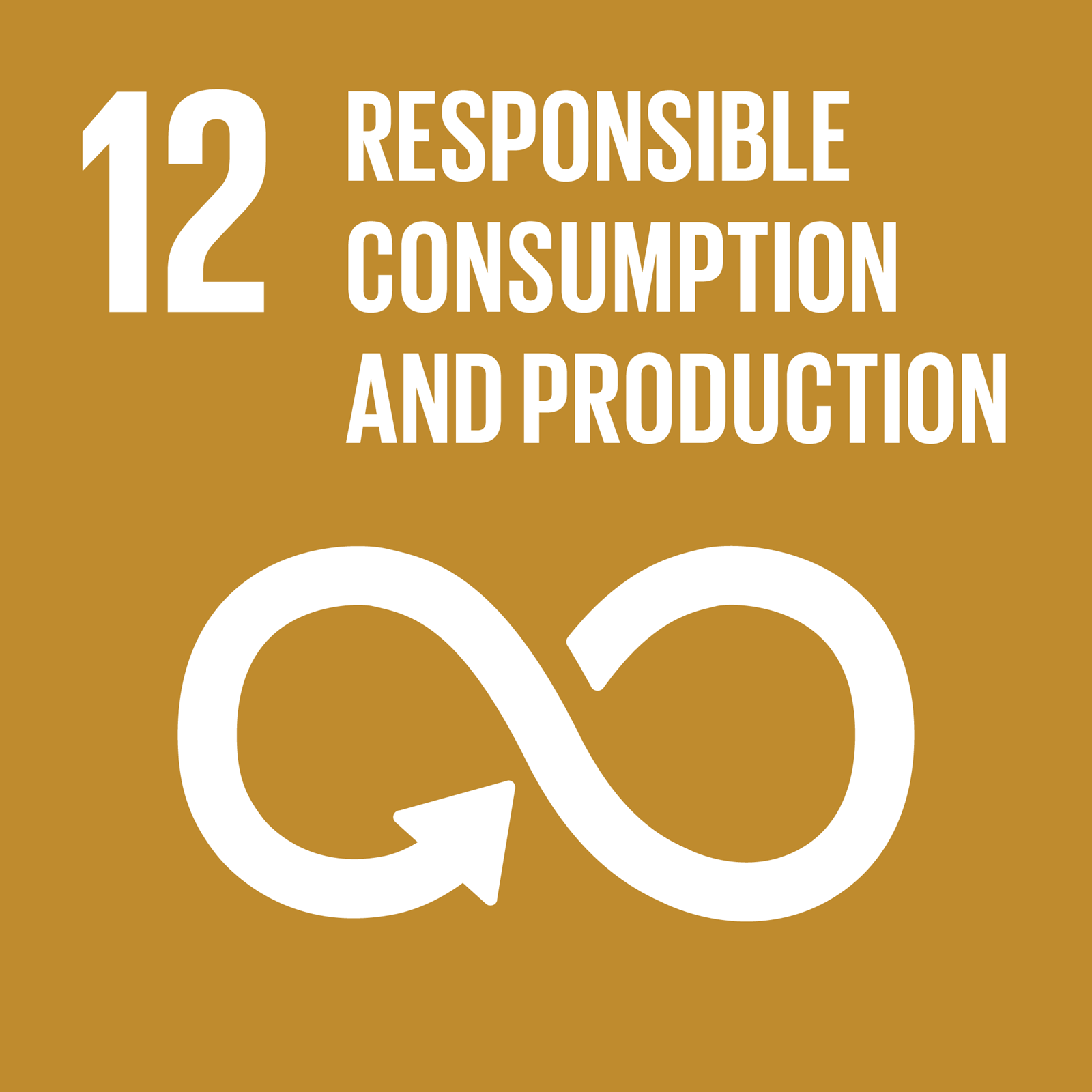
We recognize that primary production of metals is very carbon and energy intensive. To maximise the use of the produced metals, we will reduce our scrap by 20% in our central warehouses by 2040.
We will reduce our scrap in two ways:
- Improve material yield in production
- Improve reuse of scrap material in production
We will also provide materials with a reduced carbon footprint, e.g. material produced from recycled metals.
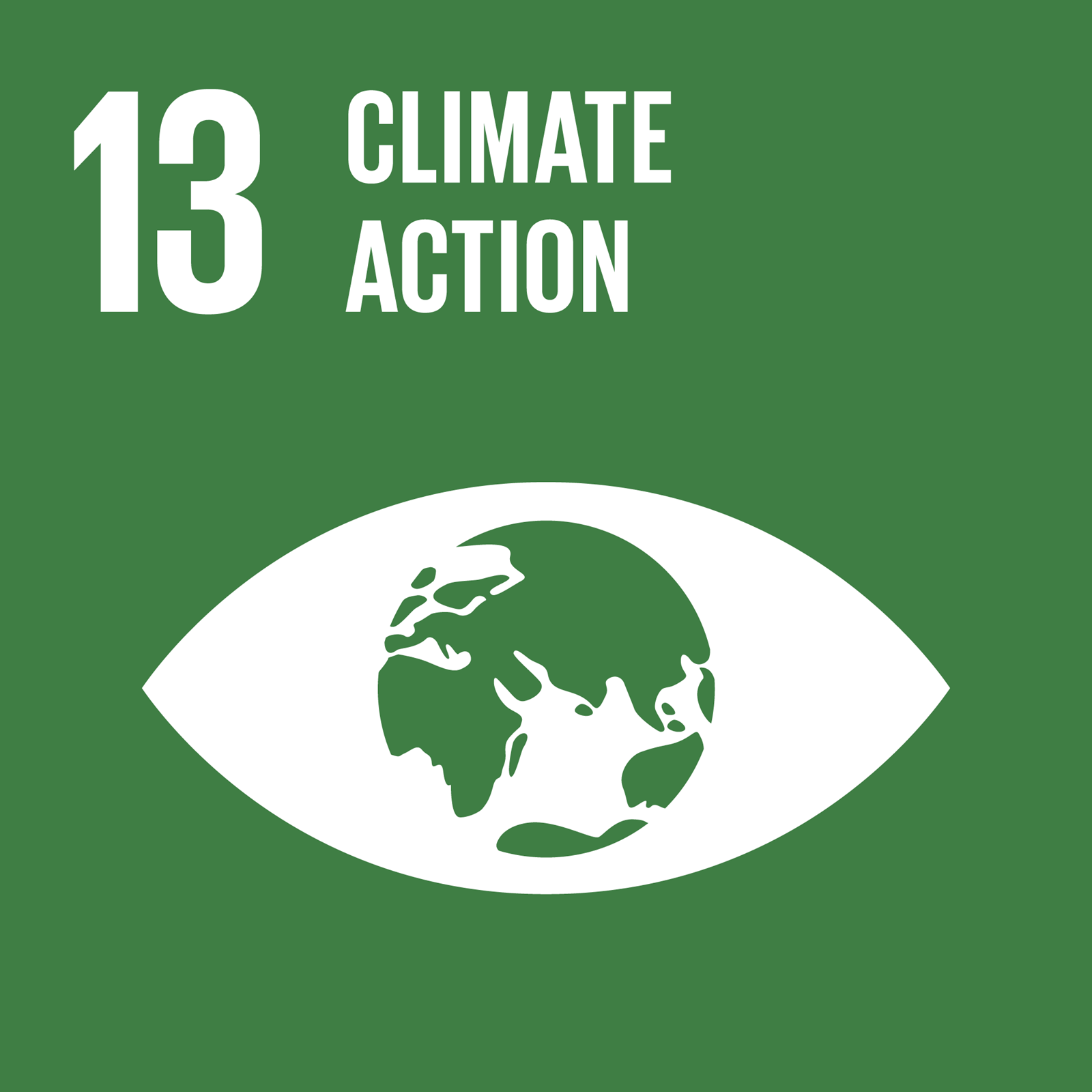
Our mission is to reduce our total CO2 emissions, within scope 1 and 2, by 80% before the year 2040.
Our main actions are:
- Reduce our direct emissions
- Invest in renewable electricity
Scope 1, 2 and 3
Our carbon reduction efforts cover scope 1, 2 and 3. We have mapped our emissions from scope 1 and 2 and are continuously initiating projects to minimise our environmental impact.
For scope 3, we have mapped all upstream activities and transportation (downstream) and continue to improve our data.
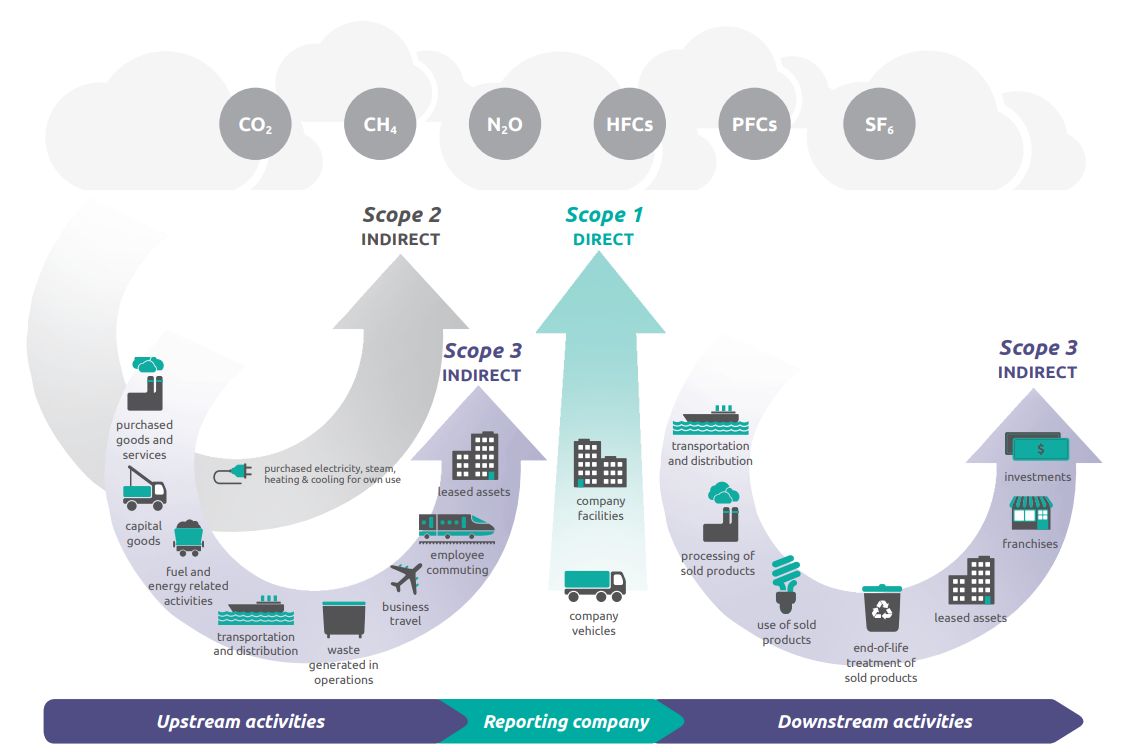
Scope 3 consists of 15 categories spanning the entire life cycle of the product, from initial mining or production to end-of-life treatment. Five of these categories are not applicable to our business and not part of our sustainability efforts.
Within the remaining 10 categories, our main focus is on transportation and distribution of goods, travelling and purchased goods and services. We have completed data collection in 7 categories.
How will we reach our goals?
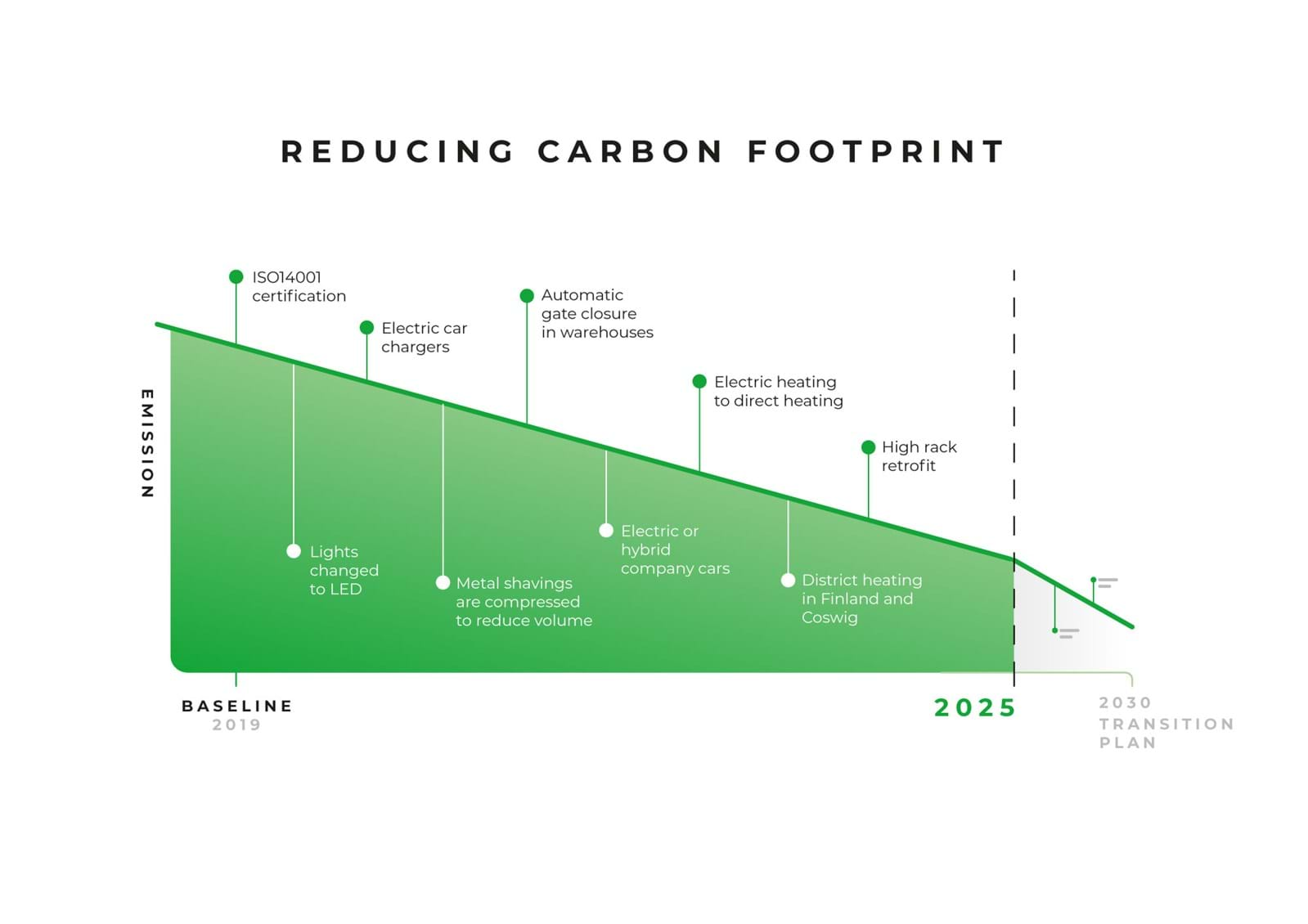
ISO 14001 and ISO 45001
Through ISO 14001 we are committed to continuously improve our impact on the environment and set clear goals.
Alumeco is currently ISO 14001 certified in Denmark, Sweden, Finland and Germany, and Aluwind is certified in Denmark, Poland and China.
Furthermore, as of 2023, we are ISO 45001 certified in our four main warehouses to ensure a continued focus on work environment and employee wellbeing.
Local projects
To reach our goals, we are approaching these issues from multiple angles - through multiple projects throughout Alumeco Group.
We have e.g. invested in a new software for our plate saws in Denmark and Germany, which helps us to save up to 5% raw material every year. In connection with this, we also developed a new policy on reusing scrap based on historic data.
We have also installed chargers for electric cars in Denmark, so customers and employees can charge their car during work hours.
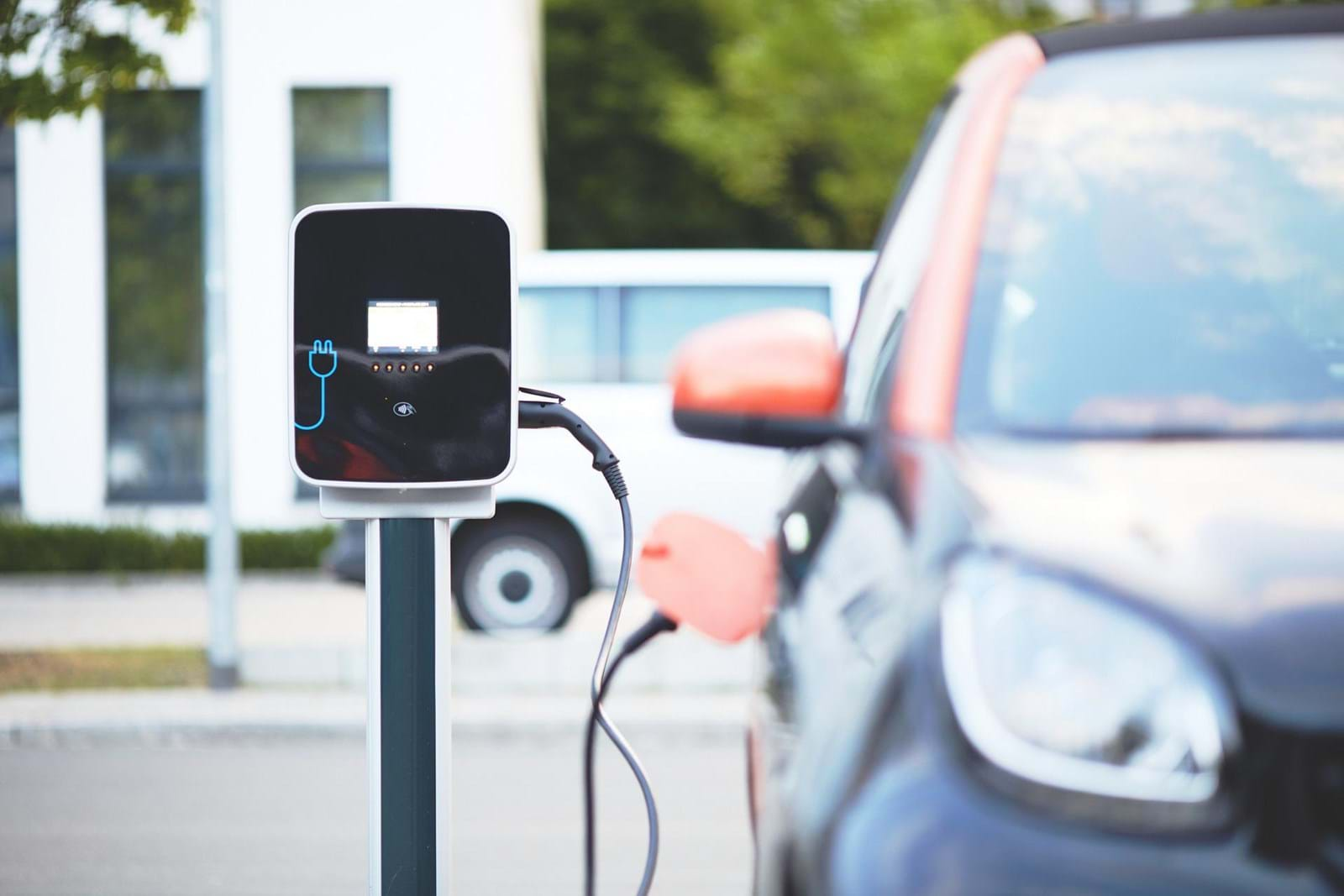
Recycling metals
The initial mining of raw materials and production of primary metal is the most significant sustainability challenge in our industry. However, a lot of metals can be recycled and reused with significantly reduced impact on the climate and environment.
Recycled aluminium
Aluminium does not exist in its pure state in nature. To produce aluminium, bauxite is mined and refined into alumina (aluinium oxide), which can then be separated into aluminium and oxide through electrolysis. The electrolysis process is very energy intensive, but once the aluminium has gone through this process once, it can be reused and recycled almost endlessly.
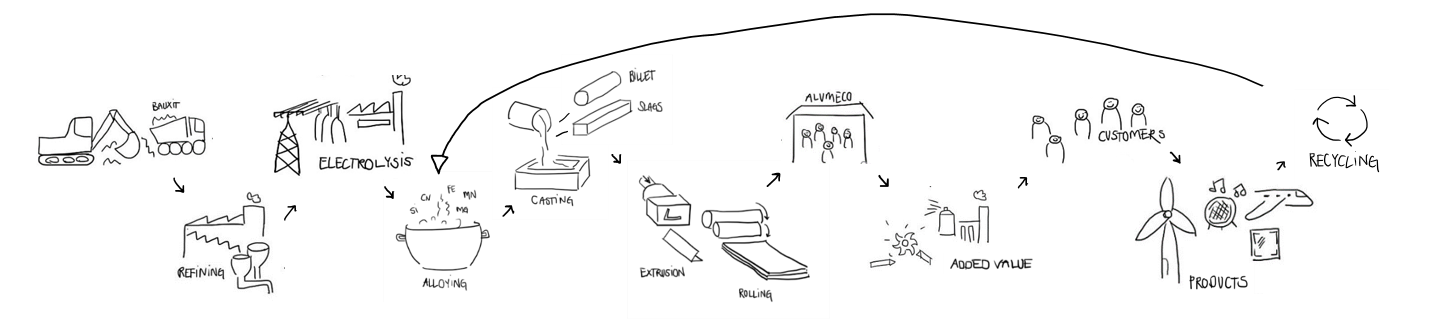
There are currently two ways to reduce the carbon footprint of aluminium:
- Using renewable energy in the production
- Increasing the scrap content
With the first option, the carbon emissions from primary aluminium production can be reduced to around 4 kg CO2/kg aluminium. In this case, the energy comes mainly from renewable sources such as wind or water.
The other option is to re-melt scrap aluminium into new material. This only requires 5 % energy compared to producing primary aluminium through electrolysis and can have a carbon footprint as low as 2.04 kg CO2/kg aluminium depending on the scrap content.
We offer a range of both types of products - reach out to us to hear more about your options and how we can help reduce your carbon footprint by choosing a different supplier or product.
Recycled copper alloys
Because copper is an essential component in the green transition, copper scrap is a very valuable material. One third of the global demand for copper is met through recycling, and in Europe the rate is approximately 50%. However, there is still untapped potential in dismantling and recycling the metals in e.g. old batteries and electric components.
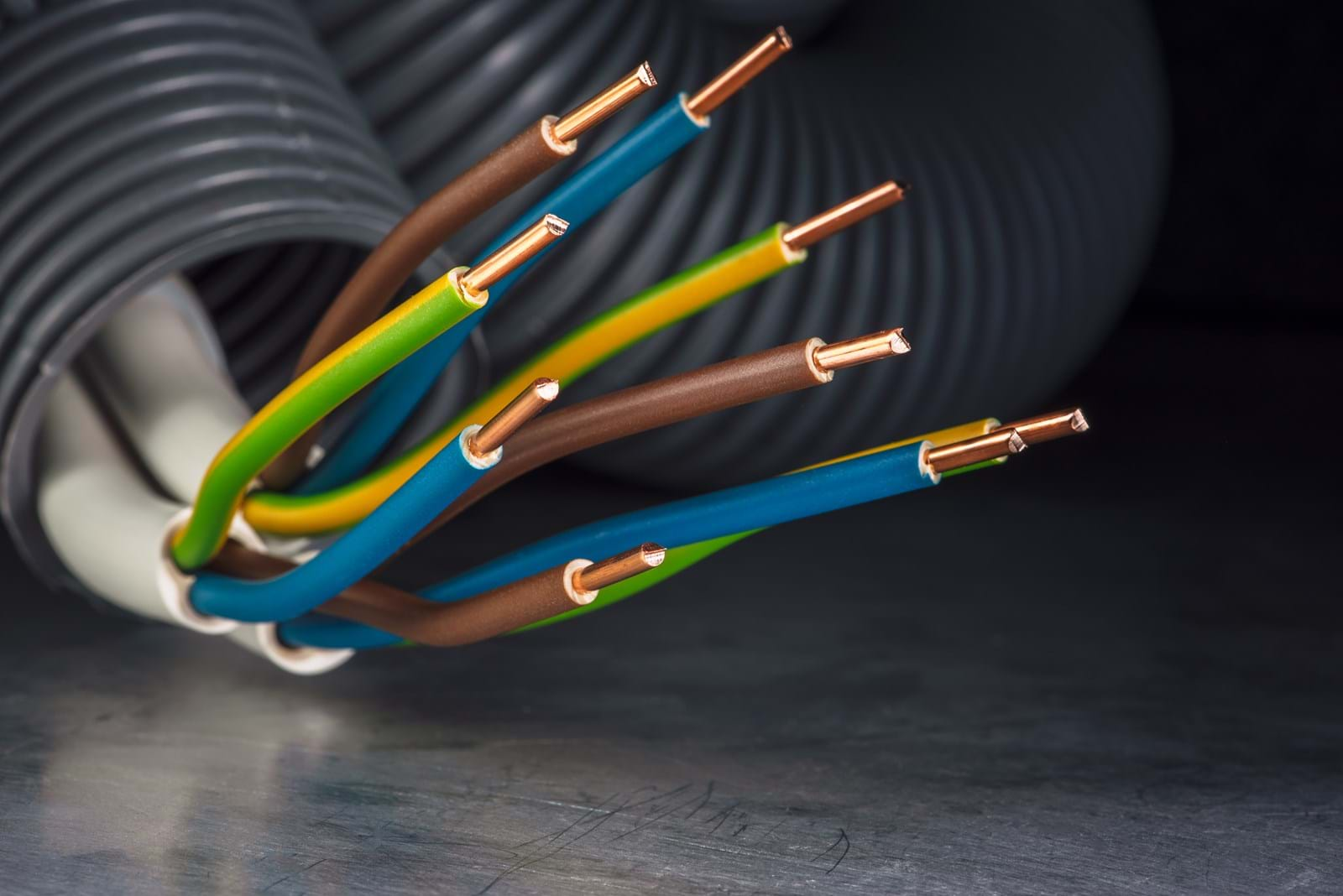
To encourage recycling, we have introduced closed loops for some of our copper/brass customers, enabling them to sell their scrap back to us in return for new metals. We intend to refine and expand this programme, but the practical and legal framework is not in place yet.
Recycled stainless steel
The most common alloying elements in stainless steel, such as nickel, chrome and molybdenum, cannot be found in nature in their pure form. This means that in addition to the initial mining process, the material then needs to be purified before it can be used in the production of stainless steel.
This proces is energy intensive, but, once produced, stainless steel can be reused many times without compromising the quality. This reduces the need for mining and purifying the raw materials.
Today, between 80 and 90% of all stainless steel produced in Europe comes from scrap metal.
Potential challenges
We recognize that our environmental footprint as a wholesaler is only a small fraction of the environmental impact of the metal industry.
Mining and producing metals is very energy and carbon intensive, and even though these emissions are not a result of our business specifically, we do carry part of the responsibility.
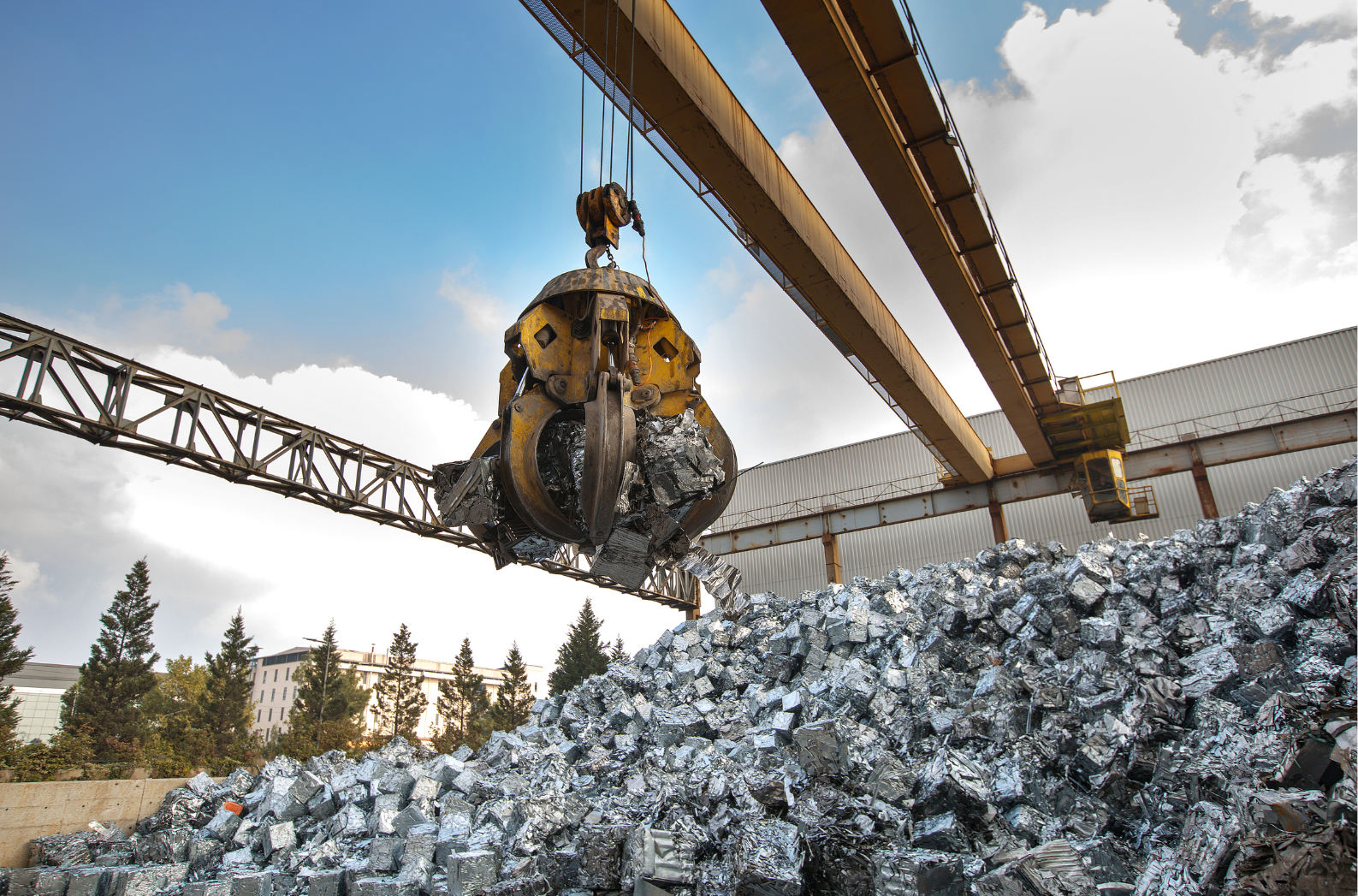
One of the ways to manufacture carbon-reduced aluminium is to increase the scrap content. However, the industry as a whole is facing a major shortage of scrap aluminium.
Aluminium can be recycled endlessly with no loss of quality, but aluminium is also very long-lasting. This combination means that the demand for aluminium is a lot higher than the available amount of scrap.
In fact, if all aluminium produced in 1990 were to be recycled in 2020, it would only cover 30% of the global demand for aluminium.
In short, even though there is a huge potential in recycling aluminium, this potential is already utilised. The big wins in the near future will instead be coming from reducing the carbon emissions from primary production of aluminium.
Similarly, the demand for copper is rising and will continue to rise with the green transition.
Copper is the best known conductor of electricity after silver, which makes copper an essential component of e.g. electric vehicles, information systems and renewable energy production. As a result, the demand for copper cannot be met through recycling alone – but with a stronger focus on closed loops and utilizing the value of copper scrap, we can increase the recycling rate of copper.